Sinkholes in Candles: Understanding, Fixing, and Preventing Them
Have you ever noticed those pesky sinkholes forming in your candles? They can be frustrating, but you're not alone! Today, we're diving into the world of sinkholes in candle making, exploring what causes them, how to fix them, and tips to prevent them from happening in the first place. Let’s get started!
What Are Sinkholes and Why Do They Happen?
Sinkholes are voids or depressions that form in candle wax as it cools. Often hidden under the surface, these imperfections can affect both the appearance and burn quality of your candles. If left unaddressed, sinkholes can lead to inconsistent burning, causing the wick to extinguish due to a lack of wax or oil to fuel the flame.
So, what causes these sinkholes? The primary reason is that wax contracts as it cools. If the cooling process is uneven or too rapid, it can create voids where the wax hasn’t fully settled. Additionally, certain types of wax, like soy wax, are more prone to sinkholes due to their natural properties. In contrast, paraffin and coconut waxes tend to have a more stable cooling process.
Identifying Sinkholes
Sinkholes might seem minor, but they can have significant consequences for your candles. Always check your finished products for signs of sinkholes, which can range from barely noticeable dents to more obvious depressions. Here are a couple of examples:
- One candle displays a clear sinkhole on the surface.
- Another has a subtle dent that might be hard to see but is still present.
It's crucial to inspect your candles carefully, as even minor sinkholes can frustrate customers and affect their overall experience.
The Role of Wax Temperature
Temperature plays a critical role in the candle-making process, especially when it comes to sinkholes. Each type of wax has a recommended pouring temperature. For instance, with 464 soy wax, the ideal pouring range is between 135 to 145°F. Pouring too hot can trap air and cause uneven cooling, while pouring too cold can lead to adhesion issues.
Here’s a quick overview of pouring temperatures for different wax types:
- Soy Wax: 135-145°F
- Paraffin Wax: 160-180°F
- Beeswax: 155-160°F
It's essential to follow your wax manufacturer's recommendations for heating and pouring temperatures to mitigate the risk of sinkholes.
Tips to Reduce Sinkholes
Here are four practical tips that can help you minimize the occurrence of sinkholes in your candles:
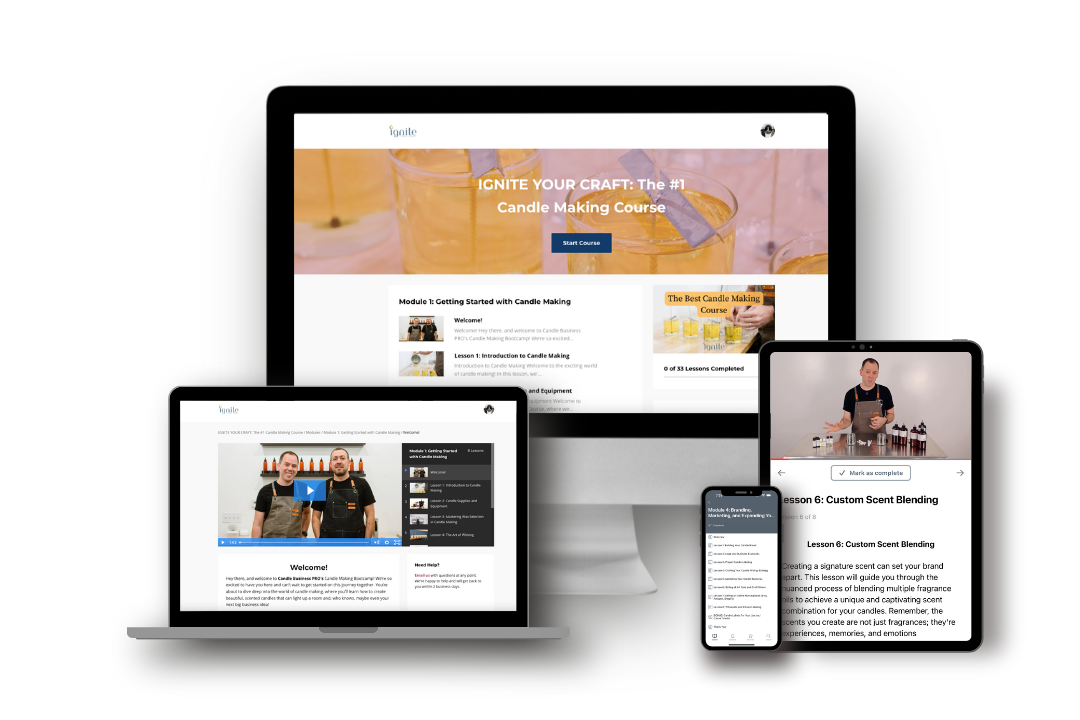
#1 Candle Making Course
We will help you make great candles you can sell! $$
Start Making Candles You Can Sell!- Pour at the Right Temperature: As mentioned, ensure you’re pouring your wax at the correct temperature for the type of wax you’re using.
- Control Your Workspace Temperature: Maintain a consistent, moderate temperature in your workspace. Avoid drafty or cold rooms that can cause your candles to cool too quickly.
- Pour Slowly and Evenly: A steady hand can help minimize air pockets, which can lead to voids as the wax cools.
- Avoid Temperature Changes: Ensure that your candle containers are at room temperature before pouring. Let your candles cool naturally in a stable environment.
Fixing Sinkholes: Two Methods
Even with all precautions, sinkholes can still occur. Fortunately, there are simple methods to fix them. You’ll need a heat gun and a skewer for these techniques.
Method 1: The Heat Gun Method
This method involves gently melting the top layer of the wax to allow it to even out and fill the sinkhole. Here’s how to do it:
- Use a heat gun to melt the surface of the candle where the sinkhole is.
- Gently move the heat gun around the top of the candle, ensuring you’re not overheating the wick or the container.
- Allow the melted wax to settle into the sinkhole, filling it up naturally.
Method 2: The Skewer Method
For larger or more troublesome sinkholes, you can use the skewer method. Follow these steps:
- Use the skewer to poke into the sinkhole, creating pathways for the melted wax to fill in.
- Apply the heat gun again to melt a thin layer of wax, allowing it to fill the newly created pathways.
- Let the candle cool and solidify before inspecting it again.
Final Steps and Quality Assurance
After you've applied one of the methods above, let your candles sit for a few minutes to harden. Check again for any remaining sinkholes or bubbles. If necessary, repeat the heating process until you achieve a smooth, even surface.
Remember, leaving sinkholes unaddressed can impact the burn performance of your candles and lead to customer dissatisfaction. By taking the time to fix them, you’re ensuring a better experience for your customers.
Key Takeaways
- Always check for sinkholes before finishing your candles.
- Pour at the right temperature for your wax type.
- Control your workspace conditions to minimize cooling issues.
- Use the heat gun method or skewer method to fix sinkholes effectively.
- Build consistent habits in your candle-making workflow to improve quality.
Conclusion
Sinkholes are a common challenge in candle making, but they’re not insurmountable. By understanding their causes and employing effective fixing methods, you can create beautiful candles that burn evenly and delight your customers. Do you struggle with sinkholes? What wax do you use? Let me know in the comments, and let’s keep the candle-making community thriving!
Stay connected with news and updates!
Join our mailing list to receive the latest news and updates from our team. We also get exclusive discounts to share.
Don't worry, your information will not be shared.
We hate SPAM. We will never sell your information, for any reason.